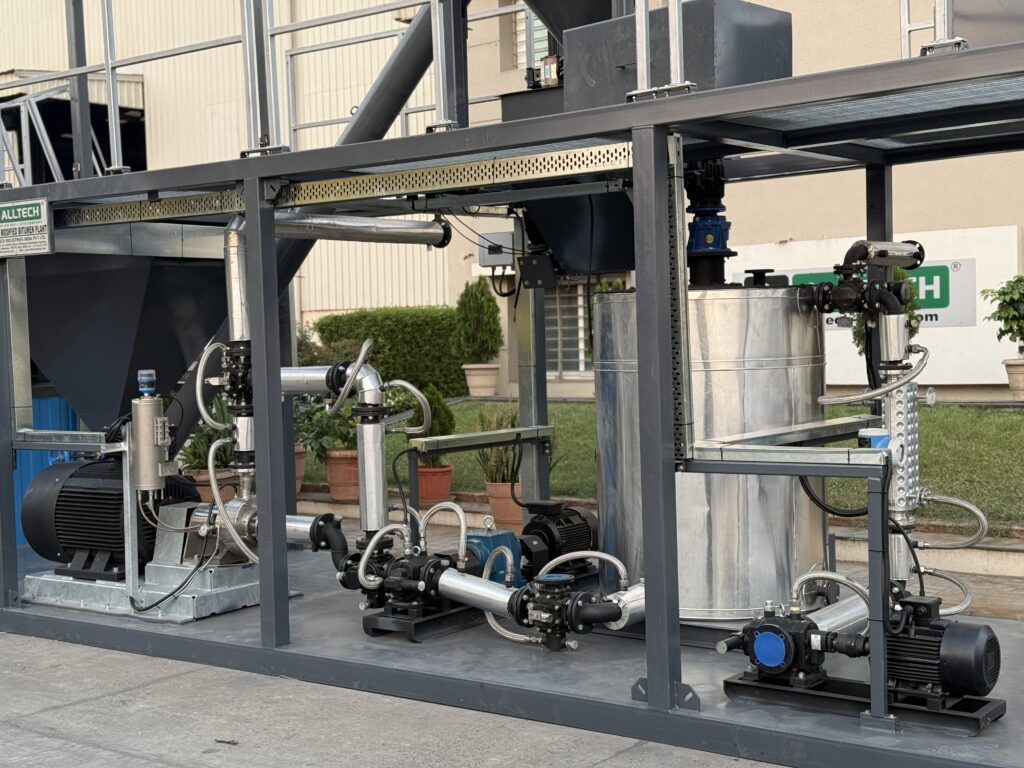
In the realm of modern infrastructure and high-performance road construction, Polymer Modified Bitumen (PMB) stands out as a key material. By enhancing the performance characteristics of conventional bitumen, PMB delivers greater elasticity, durability, and resistance to deformation—making it ideal for demanding applications.
This article offers a comprehensive look into how a polymer modified bitumen plant operates. From core components to the manufacturing process and quality control measures, we uncover the technological sophistication that powers PMB production.
What is Polymer Modified Bitumen?
Polymer Modified Bitumen is a specialized asphalt binder created by incorporating polymers—such as Styrene-Butadiene-Styrene (SBS), Ethylene Vinyl Acetate (EVA), or Crumb Rubber—into base bitumen. This modification significantly improves elasticity, cohesion, and resistance to rutting and thermal cracking.
PMB is widely used in:
- High-traffic highways
- Airport runways
- Bridges and overpasses
- Urban roadways
- Regions with extreme weather conditions
Core Components of a Polymer Modified Bitumen Plant
A well-designed polymer modified bitumen plant integrates multiple systems to ensure consistent and high-quality PMB production. Key components include:
1. Bitumen Storage Tanks
These tanks maintain base bitumen at 160°C–180°C to preserve fluidity. They feature thermal oil heating and agitators for uniform temperature distribution.
2. Polymer Feeding Unit
Solid or liquid polymers are introduced via manual or automated feeders, with precise measurement critical to batch consistency.
3. High Shear Mixer
The core of the plant, this unit ensures complete blending of bitumen and polymer. High shear mixing enables polymer swelling and even dispersion throughout the bitumen matrix.
4. Additive Dosing System
Additives such as compatibilizers, stabilizers, and anti-stripping agents are introduced to enhance storage stability and performance.
5. Colloid Mill or Homogenizer
This component refines the blend further, eliminating any remaining polymer clumps and ensuring a uniform final product.
6. Heating and Circulation System
A closed-loop system ensures continuous flow and proper temperature control throughout the manufacturing process.
7. Finished Product Storage
Final PMB is stored in insulated tanks equipped with agitators and temperature control to maintain product integrity.
The PMB Manufacturing Process: Step-by-Step
A polymer modified bitumen plant follows a structured process:
Step 1: Heating the Base Bitumen
Base bitumen is pumped and heated to the required process temperature.
Step 2: Polymer Introduction
Pre-weighed polymer is fed into the heated bitumen stream.
Step 3: Blending in High Shear Mixer
The high shear mixer disperses the polymer evenly, allowing it to integrate fully with the bitumen.
Step 4: Additive Integration
Performance-enhancing additives are introduced at controlled rates.
Step 5: Homogenization
The blend passes through a colloid mill or homogenizer for further refinement and texture uniformity.
Step 6: Quality Testing
Samples are tested for penetration, softening point, elastic recovery, and stability as per international standards.
Step 7: Storage and Dispatch
The final product is stored in heated tanks and dispatched in drums or tankers based on customer requirements.
Benefits of a Polymer Modified Bitumen Plant
Operating a polymer modified bitumen plant offers significant advantages:
- Enhanced Rut Resistance – Withstands heavy traffic loads
- Improved Elasticity – Performs well under temperature variations
- Longer Lifespan – Reduces maintenance frequency
- Superior Adhesion – Ensures better bonding with aggregates
- All-Weather Performance – Effective in both hot and cold climates
Quality Control in PMB Production
Each batch from a polymer modified bitumen plant is rigorously tested to meet standards like ASTM D5976, IS 15462, or AASHTO M320. Key quality parameters include:
- Viscosity
- Softening Point
- Penetration
- Elastic Recovery
- Storage Stability
Environmental and Operational Considerations
Modern PMB plants are designed with sustainability and efficiency in mind:
- Energy Efficiency – Thermal oil heating and insulation reduce energy loss
- Emission Control – Scrubbers and filters minimize environmental impact
- Automation – PLC or SCADA systems ensure process precision and minimize human error
Final Thoughts
As infrastructure demands continue to grow, the importance of a well-equipped and efficiently operated polymer modified bitumen plant becomes increasingly clear. PMB not only meets the performance expectations of today’s roads but also supports longer-lasting, sustainable infrastructure development.
Whether you’re a civil engineer, road contractor, or industry researcher, understanding how a polymer modified bitumen plant works helps you appreciate the innovation behind every high-performance road.